SUSTAINABILITY
WATER RECLAMATION
In 1990, we installed our first water recovery system which reclaims, filters and reuses 100% of the water used in our manufacturing processes. By continually upgrading this system, we ensure we have the latest state-of-the-art technology and most energy-efficient systems available. We save millions of gallons of water every month and eliminate all waste water discharges from our production operation.
SUSTAINABILITY
TRIM BUYBACK PROGRAMS
As a compounder, we understand plastics and what constitutes scrap vs reusable clean thermoplastics. Based on our extensive knowledge of resins and custom compounds, we are able to recycle the vast majority of our off-spec extrusion material back into future production runs. Any that cannot be used is sold to be used in other manufactured products. Nothing goes in the landfill. We work closely with our customers to buy back any reusable trim created in their production processes. They work to keep trim pieces clean and segregated and we buy it back to be reused either in their products or in other lower spec items.
SUSTAINABILITY
ENERGY CONSERVATION
Processing thermoplastics is an energy-intensive process. Our plants and warehouses are operational 24 hours a day, and require significant power for lighting and ventilation. We use energy efficient, LED lighting across all facilities that are controlled by motion detectors, reducing our power consumption and carbon footprint. We proactively upgrade our extruders, injection molders, and mechanical equipment with state-of-the-art technologies in order to reduce our power consumption and carbon footprint.
SUSTAINABILITY
SOLAR ENERGY
In 2010, we made our largest investment ever in sustainability with the construction of a massive solar array at our facility in California. This project required a multi-million-dollar investment and a significant reallocation of available space - and we are very proud of the results. Our solar array system generates 800 Megawatt-Hours annually which represents about one third of our power consumption at this facility. Due to the success of this initiative, we equipped our Missouri plant with a comparable solar array in 2019.
SUSTAINABILITY
THERMAL EFFICIENCY
Processing thermoplastics requires significant cooling and refrigeration resources. Across our production plants, we strive to engineer the most efficient plant cooling systems for each particular environment, to minimize our power consumption and carbon footprint at each plant. For example, our high-altitude facility in Nevada uses an innovative hybrid cooling system that combines evaporative cooling and advanced refrigeration equipment to provide the most efficient cooling solution for any given ambient condition and season, reducing our overall power consumption by 40% annually.
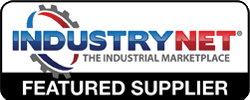
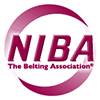

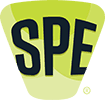